XKH series five-axis linkage blade machining center is a high-efficiency, high-precision five-axis linkage blade machining center designed and developed by applying international advanced technology to meet the needs of various blade processing.The machine tool is suitable for processing various blades and various narrow and long parts. It covers the processing range of blades of various purposes, specifications and materials, and is widely used in energy and other industries.Structural features: 1. Double drive of the head and tail frames: both the head frame and the tail frame are driven by torque motors, with fast response and no gap; to meet the requirements of high rotation precision, fast speed, and quick differential compensation response required by the machining of aviation blades.2. Full-closed-loop feedback measurement: Linear coordinates can use precision linear grating ruler (optional), and rotary and swing coordinates can use precision angle encoders.3. High-power precision electric spindle: The machine tool adopts precision electric spindle, which has high power, high speed, high rotation accuracy and good quick response, which improves the transmission efficiency; the spindle taper hole HSK63 ensures good rigidity of the tool holder and taper hole at high speed, Improve machining accuracy.4. Precision transmission configuration: The linear axis is driven by a precision ball screw and a precision linear guide rail, and the Z-axis double screw is synchronously driven. The transmission rigidity is strong, which improves the rigidity of the machine tool.5. Full protection safety structure: Integral machine protection; the linear axis is equipped with a stainless steel guide rail protective cover; the electrical control cabinet adopts a fully enclosed structure, which is effectively dust-proof, oil-proof, and has good sealing; it is equipped with a safety door lock to realize power-off when opening the door.6. Large-capacity tool magazine: configure a large-capacity tool magazine according to customer processing requirements, with automatic tool magazine door, automatic tool change without manipulator, and tool change at will.7. U-axis servo control: Tailstock U-axis servo control, adjust the relative size of the head and tail frame according to the size of the workpiece, the adjustment range is 450mm.8. Precision large-flow cooling and filtering system: large-flow tool cooling, equipped with cutting fluid filtering device, the flow rate is not less than 50L/min.Technical parameters: Project unit XKH1600 XKH800 XKH800A XKH400A Working range The maximum distance between the headstock and tailstock spindle end face mm 1600 800 500 The maximum turning radius of A axis mm 440 300 X, Y, Z axis mm 2200/400/400 1250/400/400 1560 /500/400 500/300/400 A axis n×360° B axis ±40° Feed rapid movement range (X/Y/Z) m/min Max.12 Max.12 A axis r/min Max.45 Max .80 Max.120 B-axis r/min Max.12 Max.30 Spindle Spindle speed rpm 60-10000 60-15000 Spindle taper hole HSK63A Spindle power Kw 25 20.5 Tool magazine Tool magazine capacity pcs 12/16 Maximum tool diameter mm φ63 max Tool length mm 180 180 Power source full load current A 200 Compressed air working pressure mpa >0.6 Power requirements 380 (1±10%) V 50HZ Machine size Machine tool dimensions mm 4260×2600 3314×2600 3630×2720 3120×2818 Machine tool footprint Size mm 6100×5200 5200×5200 5470×5200 5400×5900 Machine tool height mm 2600 2432 Machine tool net weight Kg 12000 10000 8000 Control system Siemens Main configuration: 1. Resin sand casting. 2. Three-axis ball screw Taiwan Shangyin.3. Precision lock nut.4. Spindle made in Taiwan (Master), Japan NSK bearings, spindle pulley and belt.5. Supercharged cylinder (Shangpin) made in Taiwan.6. Imported bearings (Japan NSK).7. Domestic high-quality couplings.8. X, Y, Z (bottom) stainless steel rail protection.9. Imported electronic lubrication pump (Japanese river valley).10. The domestic cooling system includes a water pump and a water tank.11. Pneumatic components (German AirTAC).12. Headstock weight hammer counterweight.13. Optional: automatic spiral chip removal function.14. System brands are optional: FANUC, Guangshu, Siemens, Kaind, Mitsubishi.15. Disc type tool magazine BT40-T24 (Taiwan Zhenshang).16. With spindle oil cooling function, center air blowing.17 Main electrical appliances: SCHNETDER (Schneider).
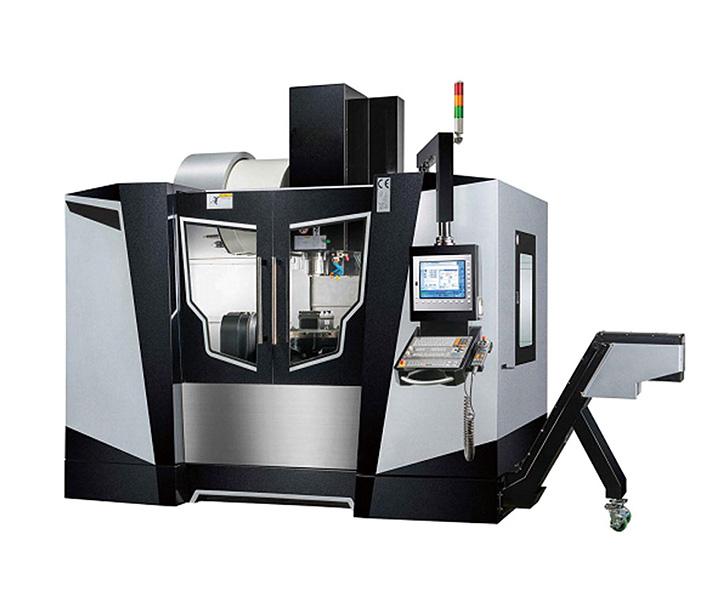